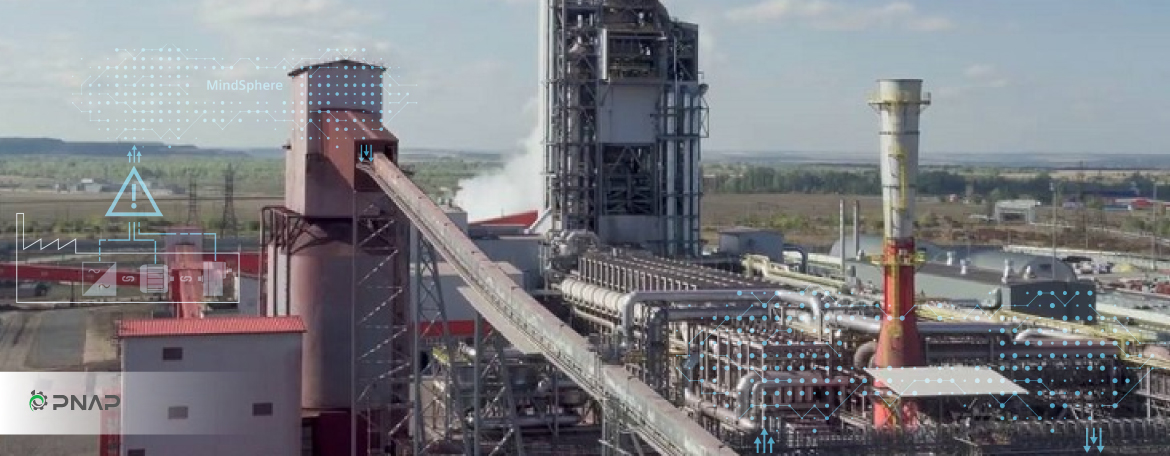
فرایند احیا مستقیم آهن اسفنجی به روش midrex
به فرآیند تولید فولاد با استفاده از سنگ معدن آهن (Steel ore) و یا قراضه (Scrap) فولادسازی گفته میشود. در این فرآیند ناخالصیهایی از قبیل نیتروژن، سیلیکن، فسفر، سولفور و مقادیر اضافی کربن همراه با اکسیژن ترکیب شده با آهن به روشهای فیزیکی (ذوب) و شیمیایی (واکنش) از آن حذف میشود. سپس ترکیبات مختلفی شامل منگنز، نیکل، کروم، کربن و وانادیوم به تناسب مشخصات محصول مورد نظر به آن اضافه شده تا در نهایت فولاد با کیفیت بالا و پایدار حاصل میشود. مسیر صنعتی شدن تولید فولاد از اواسط قرن 19 میلادی شروع شد. در دهههای 1850 و 1860 میلادی، فرآیندهای بسمر (Bessemer Process) و زیمنس-مارتین (Siemens-Martin Process) تولید فولاد را به یک صنعت سنگین و پیچیده تبدیل کرد.
در جهان امروز، فولاد مهمترین نقش را در توسعهی زیرساختهای یک کشور ایفا کرده و یکی از اصلیترین ارکان یک جامعهی صنعتی میباشد. در شکل زیر میزان تولید فولاد 20 کشور برتر تولید کنندهی فولاد دنیا در سال 2022 در واحد میلیون تن نمایش داده شده است. همانطور که مشاهده میشود، کشور چین با تولید بیش از هزار میلیون تن فولاد در سال 2022 رتبه اول دنیا در این صنعت را از آن خود کرده است. همچنین کشور ایران با تولید بیش از 30 میلیون تن فولاد در رتبهی دهم دنیا قرار گرفته است.
امروزه بخش عمدهی تولید فولاد در جهان، با استفاده از دو روش کوره بلند-کورهی اکسیژن قلیایی (BF-BOF) و یا احیای مستقیم-کورهی قوس الکتریکی (DRI-EAF) انجام میشود. در روش BF-BOF، ابتدا آهن خام با درصد خلوص بالا با استفاده از کورهی بلند تولید شده و سپس فرآیند فولادسازی در کورهی اکسیژن قلیایی صورت میگیرد. مشابه این روش، در روش DRI-EAF نیز، آهن خام در کورهی مربوطه با استفاده از واکنشهای احیای مستقیم تولید شده و سپس با استفاده از کورهی قوس الکتریکی فرآیند فولادسازی تکمیل میشود. در شکل زیر فرآیند این دو روش به صورت گرافیکی نمایش داده شده است.
طبق آمار موجود در سال 2021، سهم هر کدام از این روشها در مقدار فولاد تولید شده در کشورهای جهان و ایران در جدول زیر ارائه شده است. مشاهده میشود که در دنیا، بیش از 70 درصد فولاد تولیدی با استفاده از مسیر BF-BOF و کمتر از 30 درصد آن از روش DRI-EAF میباشد. اما این نسبت در کشور ایران به طور قابل توجهی معکوس میباشد. بر این اساس، بیش از 90 درصد فولاد تولیدی در ایران از روش DRI-EAF بوده و مابقی آن از روش BF-BOF تولید میشود. شایان ذکر است این آمار در مورد ایران به صورت تخمینی (Estimated) ارائه شده است.
تولید فولاد با استفاده از روش DRI-EAF با استفاده از تکنولوژیهای مختلفی صورت میگیرد. در شکل زیر سهم تکنولوژیهای مطرح این حوزه در تولید فولاد از روش DRI-EAF در جهان را در سال 2021 نشان میدهد. مشاهده میشود که تکنولوژی MIDREX به تنهایی بیش از 59 درصد از تولید فولاد با این روش را به خود اختصاص داده است.
بر این اساس، با توجه به اهمیت ویژهی روش تولید فولاد DRI-EAF در ایران و نیز سهم حداکثری تکنولوژی MIDREX در این روش، در ادامه به بررسی بیشتر جزئیات پیرامون این تکنولوژی پرداخته شده است.
تاریخچه فرآیند
در فرآیند تولید فولاد به روش احیای مستقیم MIDREX جهت احیای آهن خام از گاز طبیعی استفاده میشود. تکنولوژی پایهی این فرآیند توسط شرکت Midland-Ross که بعدها به MIDREX Technologies تغییر نام داد، ارائه شده است. نمونهی آزمایشی این فرآیند در ابتدا در شهر Toledo در ایالت Ohio آمریکا در سال 1967 ساخته شد. پس از آن، اولین واحد تجاری این فرآیند نیز با ظرفیت 150 هزارتن در سال، در سال 1969 در شهر Portland در ایالت Oregon آمریکا ایجاد شد. در ادامه تصویری از این واحد ارائه شده است.
در سال 1978، زمانی که شرکت Kobe Steel در قطر، ساخت یک واحد با ظرفیت تولیدی سالانه 400 هزارتن را به اتمام رساند، این فرآیند هنوز از نظر تکنولوژی نابالغ بود. در سالهای بعد، شرکت Kobe Steel اصلاحات قابل توجهی در زمینههای طراحی، تکنولوژی و پایداری این فرآیند ایجاد کرد. از طرف دیگر، شرکت MIDREX Technologies نیز اقدامات بهبود دهندهی زیادی بر روی واحدهای ساخته شده در کشورهای مختلف اعمال کرد. در مجموع این تغییرات در اوایل دههی 1980، باعث تکمیل و نهایی شدن ساختار و تکنولوژی این فرآیند شد.
در سال 1984، زمانی که شرکتهای MIDREX Technologies و Kobe Steel همکاری خود را آغاز کردند، بیشترین ظرفیت تولید یک واحد 600 هزارتن در سال بود. در سالهای بعد، بهینهسازیهای صورت گرفته در اثر همکاری این دو شرکت، باعث شد تا ظرفیت تولید به صورت چشمگیری افزایش پیدا کند، به طوری که در سال 2007 این مقدار به حدود 1.8 میلیون تن در سال رسید.
محصول فرآیند
محصول فرآیند MIDREX عبارت است از آهن احیا شده به روش مستقیم که با نام کوتاه شدهی DRI (Direct Reduced Iron) شناخته میشود. در این فرآیند، با استفاده از یک گاز ریفورمینگ تولید شده از گاز طبیعی، آهن خام تبدیل به DRI میشود. DRI نیز به طور معمول به عنوان خوراک کورهی قوس الکتریکی (EAF) مورد استفاده قرار میگیرد. پس از حذف اکسیژن از آهن خام، حفرههایی بر روی محصول DRI باقی میماند که به همین دلیل به آن آهن اسفنجی یا Spong Iron نیز گفته میشود. این محصول در تصویر زیر نمایش داده شده است.
حال اگر این حفرهها با رطوبت یا هوا تماس پیدا کرده و یا پر شوند، میتواند باعث اکسید شدن مجدد آهن و کاهش خلوص محصول DRI شده و تولید حرارت و یا ایجاد آتش کند. این امر، انتقال محصول DRI و یا ذخیرهسازی آن در هوای آزاد و یا برای مدت طولانی را با مشکل مواجه میکند. برای حل این موضوع، Kobe Steel تکنولوژی را توسعه داد تا بر اساس آن، محصول نهایی DRI در محدودهی دمای 700 درجهی سانتیگراد به صورت Briquette فشردهسازی شود. این نوع محصول با نام کوتاه شدهی HBI (Hot Briquette Iron) شناخته میشود.
با استفاده از این روش، دانسیتهی ظاهری محصول DRI که معادل 3.4 تا 3.6 تن بر مترمکعب میباشد، به حدود 5 تا 5.5 تن بر مترمکعب افزایش مییابد. پیش از ارائهی این تکنولوژی، سایتهای تولید محصول DRI میبایست در محدودهی کارخانههای تولید فولاد ایجاد میشد. اما با توسعهی صورت گرفته و امکان تولید محصول به صورت HBI، میتوان واحدهای تولید محصول DRI را جهت دستیابی به بهینگی اقتصادی، در جایی که قیمت گاز طبیعی، آهن خام و یا انرژی پایینتری دارد، احداث کرد. این امکان منجر به افزایش قابل توجهی در تعداد واحدهای فرآیندی بر مبنای تکنولوژی MIDREX در سراسر جهان شد. در شکل زیر میتوان تفاوت این دو نوع محصول را مشاهده کرد.
شرح فرآیند
در ابتدا خوراک فرآیند در دو حالت Lump ore و یا Pellets از بالای Shaft Furnace وارد میشود. خوراک وارد شده پس از احیا در داخل کوره، از پایین آن خارج میشود. گاز احیای مورد استفاده توسط نازلهای تعبیه شده در وسط برج به داخل آن دمیده شده و به سمت بالای برج از میان جریان خوراک جامد عبور میکند. گاز خنک کننده نیز که در بخش پایین کوره در حال گردش است، محصول DRI را خنک میکند. واکنشهای احیای شناخته شدهی زیر در اثر تماس گاز احیای سنتز با خوراک ورودی، در کوره رخ میدهد.
گاز خروجی از بالای کوره با استفاده از یک Scrubber، تمیز و خنک شده و سپس با گردش مجدد مورد استفاده قرار میگیرد. این جریان گازی حاوی دی اکسید کربن و آب بوده که توسط کمپرسور فشردهسازی میشود. در ادامه این جریان با جریان گاز طبیعی مورد استفاده در بخش ریفورمینگ ترکیب شده و پس از پیشگرم شدن به راکتور ریفورمینگ تزریق میشود. این جریان ترکیب شده، با عبور از هزاران لولهی پر شده از کاتالیست نیکل، بر مبنای واکنشهای زیر به گاز سنتز که به عنوان گاز احیا استفاده میشود، تبدیل میشود.
در شکل زیر، نمایش سادهای از فرآیند تولید فولاد به روش احیای مستقیم با استفاده از تکنولوژی MIDREX ارائه شده است.