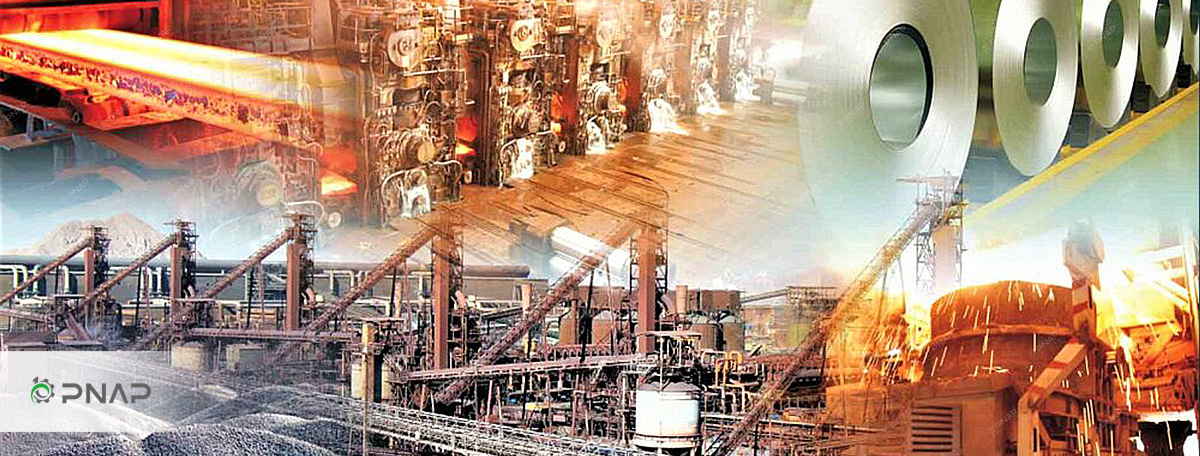
سیستم اتوماسیون یکپارچه زنجیره فولاد
آهن را می توان در زمره پر مصرف ترین فلزات در صنایع مختلف به شمار آورد. این فلز پرکاربرد ۹۵ درصد ذخایر فلزات تولید شده در دنیا را به خود اختصاص داده است. دلایل مختلفی برای بالا بودن میزان مصرف آهن وجود دارد که مهم ترین آن ها فراوانی، سهولت کار، استحکام زیاد و قیمت مناسب آهن و محصولات تولید شده از آن است.
کلیه مراحلی که سنگ آهن استخراج از معدن طی می کند تا به فولاد تبدیل شود، زنجیره فولاد نامیده می شود. این مسیر پیچیدگی و دشواری های مختلفی دارد که با استفاده از قابلیت های اتوماسیون می توان به راحتی بر آن ها فائق آمد. ارتقا کیفیت محصول تولید شده و بهبود فرآیندهای عملکردی در کنار کاهش هزینه ها از جمله مهمترین دلایل اتوماسیون زنجیره فولاد است.
شرکت پناپ به عنوان ارائه دهنده خدمات اتوماسیون صنعتی و طراح سیستم های کنترل DCS، با سابقه حضور چندین ساله در صنایع معدنی و اشراف کامل به فرایند تولید فولاد، اقدام به ارائه خدمات اتوماسیون زنجیره فولاد کرده است.
اهمیت اتوماسیون زنجیره فولاد
اتوماسیون صنعتی از بدو تولد به صورت گسترده مورد توجه صنایع مختلف قرار گرفته است. هر چقدر پیچیدگی یک فرآیند و مراحل لازم تا رسیدن به محصول نهایی بیشتر باشد، ضرورت استفاده از اتوماسیون صنعتی بیشتر می شود. در چرخه تولید فولاد بخش های حساس زیادی وجود دارند که نیاز به کنترل دقیق دارد. از کنترل عملکرد آسیاب های سنگین گرفته تا دمای کوره ها و عملیات حرارتی از جمله مراحلی است که نیاز به کنترل دقیق دارد.
اتوماسیون زنجیره فولاد ضمن اجرای دقیق همه فرآیندهای مورد نیاز، کیفیت محصول نهایی را تضمین می کند و مزایای دیگری نیز برای سرمایه گذاران به ارمغان می آورد. از جمله مزایای استفاده از اتوماسیون در کارخانه تولید فولاد می توان به موارد زیر اشاره کرد:
- بهینه سازی فرآیندها و ارتقا کیفیت محصول
- کاهش چشمگیر هزینه انرژی با مدیریت دقیق مصرف
- کاهش دور ریز مواد اولیه و محصولات تولیدی
- کاهش وابستگی به نیروی انسانی متخصص
- افزایش بهره وری و تولید
- کاهش چشمگیر هزینه های تعمیر و نگهداری
- و …
مزایای زیادی که در سایه اتوماسیون تولید فولاد حاصل می شود، استفاده از این تکنولوژی در زنجیره فولاد را توجیه پذیر و بلکه ضروری می کند. در ادامه به صورت خلاصه به معرفی مراحل مختلف زنجیره فولاد می پردازیم.
زنجیره تولید فولاد
تولید فولاد از زمان انقلاب صنعتی در اواسط قرن نوزدهم آغاز شد. در طی این سال ها روش های تولید فولاد به صورت چشمگیری تکامل یافته است. روش های مدرن صنایع فولاد بر اساس فرآیند بسمر که بیش از 150 سال پیش ابداع شد پایه ریزی می شوند.
صنایع تولید فولاد از مواد خام سنتی (آهن) و یا مواد بازیافتی به عنوان ماده اولیه استفاده می کنند. با در نظر گرفتن این موضوع، زنجیره تولید فولاد را به 7 مرحله کلی می توان تقسیم کرد.
مرحله 1 – تولید کنسانتره آهن
از آنجایی که آهن جزء اصلی فولاد است، اولین گام فرآیند با تولید آهن برداشته می شود. پس از استخراج سنگ معدن و خردایش اولیه، فرآوری و پرعیار سازی سنگ آهن در کارخانه کنسانتره صورت می گیرد. فرآیند تولید کنسانتره آهن پیچیدگی زیادی دارد. جالب است بدانید تولید کنسانتره آهن به عنوان یک صنعت مستقل نیز شناخته می شود. از جمله بخش های اصلی اتوماسیون زنجیره فولاد، اتوماسیون خط تولید کنستانتره آهن است که توسط شرکت پناپ انجام می شود.
مرحله 2 – تولید آهن
در این مرحله سنگ آهن، آهک و کک را در کوره بلند قرار داده و ذوب می کنند. خروجی این کوره آهن مذاب نام دارد. آهن مذاب هنوز حاوی حدود 4 تا 4.5 درصد ناخالصی هایی مانند کربن است که به نوبه خود فلز را شکننده می کند. بنابراین حذف این ناخالصی ها از آهن مذاب ضروری است. در مرحله بعد این ناخالصی ها از آهن مذاب جدا می شوند.
مرحله 3 – تولید فولاد اولیه
سومین مرحله زنجیره فولاد، تولید فولاد اولیه است. دو روش اصلی برای ساخت فولاد اولیه وجود دارد که عبارتند از:
- ساخت فولاد بر پایه اکسیژن (BOS)
- کوره های آرک الکتریکی (EAF)
در روش BOS ضایعات (بازیافت) فولاد به کوره آهن مذاب اضافه می شود. سپس طبق فرآیند بسمر، فشار اکسیژن اضافه می شود تا ناخالصی ها از آهن مذاب جدا شوند.
در روش EAF، فولاد بازیافتی به همراه آهن مذاب به کوره قوس الکتریکی وارد می شود. سپس تا حدود 1650 درجه سانتیگراد گرم و به فولاد درجه بالاتر تبدیل می شود.
مرحله 4 – ساخت فولاد ثانویه
در مرحله بعد، ترکیبات فولاد مذاب تازه تشکیل شده باید تنظیم شود تا ترکیب فولاد استاندارد ایجاد شود. این کار با دستکاری دمایی (عملیات حرارتی) و یا حذف عناصر خاص انجام می شود. این مرحله شامل فرآیندهایی مانند گاز زدایی، هم زدن، تزریق حباب آرگون و … است.
مرحله 5 – ریخته گری
پنجمین مرحله زنجیره فولاد، ریخته گری فولاد مذاب تولید شده است. در این مرحله فولاد مذاب خالص شده را در قالب های خنک کننده می ریزند. این قالب های به سرعت خنک می شوند. پس از سرد شدن فولاد ریخته گری شده، بسته به کاربرد و نیاز قالب ها را به طول دلخواه برش می دهند. به عنوان مثال اسلب برای تولید ورق، بلومز برای تولید تیرآهن و بیلت برای تولید مصنوعات بلند مانند سیم ها استفاده می شود.
مرحله 6 – شکل دهی اولیه
در این مرحله اسلب ها و بیلت ها معمولاً به روش نورد گرم به اشکال مختلف تبدیل می شوند. سپس محصولات نورد گرم، به شکل ورق، شمش های بلند، لوله های بدون درز و محصولات ویژه برای آخرین مرحله پردازش آماده می شوند.
مرحله 7- فرآیند ساخت و شکل دهی نهایی
در آخرین مرحله زنجیره فولاد، از انواع تکنیکهای شکلدهی ثانویه از جمله ماشینکاری، اتصال و پوشش دادن استفاده می شود تا محصولات با شکلها و ویژگیهای مورد نیاز تولید شوند. خروجی آخرین مرحله زنجیره، به عنوان مواد اولیه صنایع مختلف مورد استفاده قرار می گیرد.
سخن پایانی
فرآیند زنجیره فولاد شامل 7 مرحله مختلف است که در بالا به اختصار معرفی شدند. هر کدام از این مراحل پیچیدگی های متفاوتی دارند. استفاده از قابلیت های اتوماسیون صنعتی برای مدیریت این زنجیره پیچیده، علاوه بر اینکه شما را از استخدام تعداد زیادی نیروی متخصص بی نیاز می کند، هزینه های شما را کاهش می دهد و بهره وری کلی سیستم را افزایش می دهد. برای اتوماسیون زنجیره فولاد یا بخش های مختلف آن، به شرکت پناپ اعتماد کنید. ما دانش کافی برای پیاده سازی نیازهای شما را داریم. همین الان جهت کسب اطلاعات بیشتر با کارشناسان ما تماس بگیرید.